Generally
The liquid manure ordinance, liquid manure storage, nutrient balance and the application of liquid fermentation residues are presenting biogas operators with ever greater challenges. Due to further reduced deployment times, even more storage volume must be kept available, higher storage volume is associated with high investment costs and possibly a reclassification in the Major Accidents Ordinance.
Shorter deployment times lead to even higher costs. All of this is flanked by soil compaction, road strain, nitrogen loss, provision of cost-intensive application technology, additional workload and costs. Exhaust gas drying not only represents an economically very interesting solution, but also improves the overall situation of the biogas plant significantly and is active environmental protection. Emissions are significantly reduced in the process.
The exhaust flow contains 50% of the thermal waste heat of a CHP. In most cases, this is routed unused through the exhaust pipe into the atmosphere. With the exhaust gas flow of a CHP alone, on average 50% of the entire fermenter mass can be dried from e.g. 7% dry substance to 90% dry substance. This reduces overall storage volume by half 50% while reducing yield.
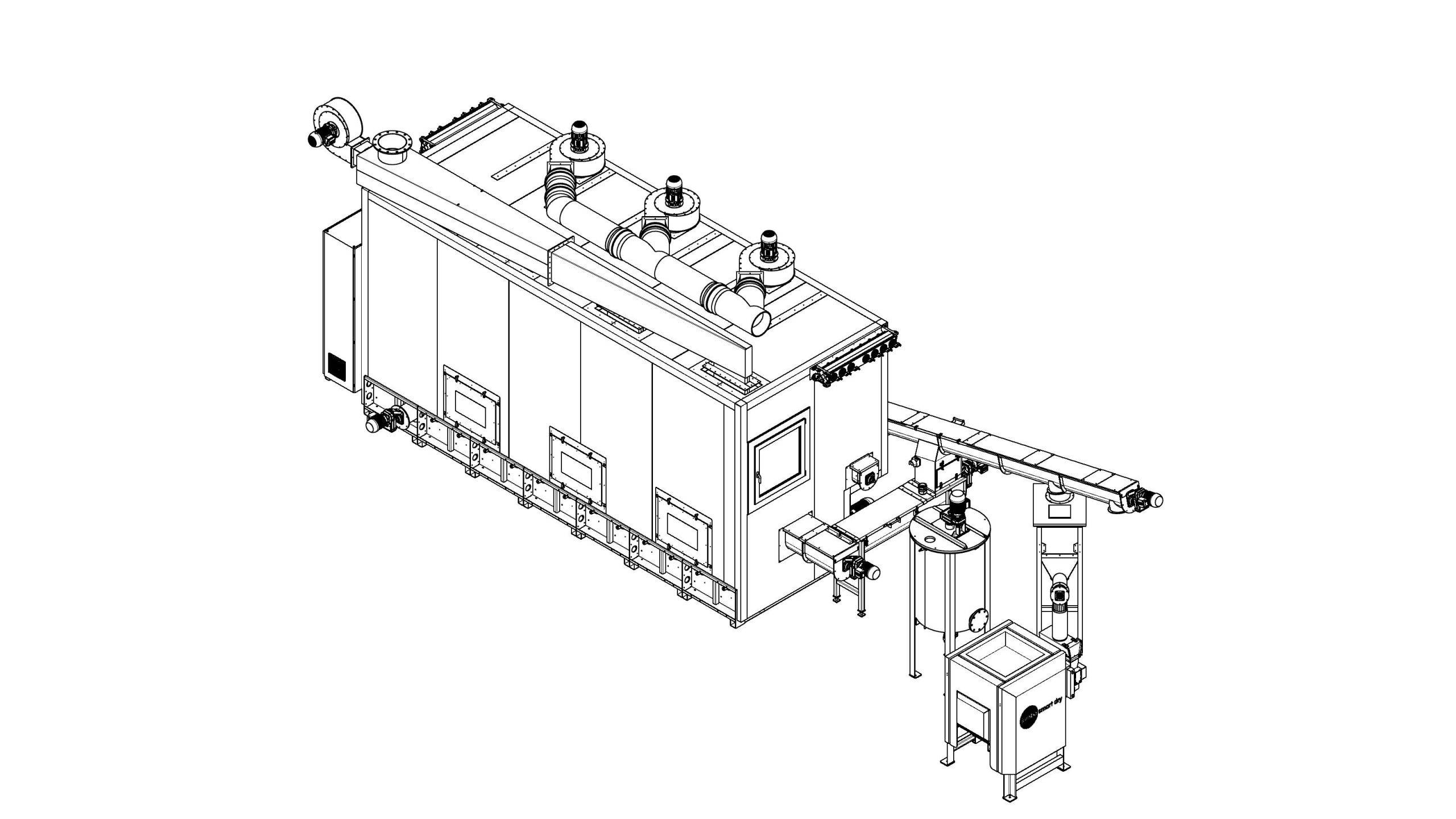
Digestate drying
Our exhaust gas drying is the ideal solution to these problems. The exhaust gas flow contains 50% of the thermal energy of your CHP. With this energy, some of which escapes unused into the atmosphere via the exhaust, a good 50% of the liquid fermenter mass can be dried in a NAWARO standard system. While the liquid evaporates completely and is released into the atmosphere, all nutrients remain concentrated in the dried digestate. You have a valuable fertilizer for your own area or for marketing.
In the drying process, the hot exhaust gases from your CHP are fed into the material cloud of the dryer. Due to the high temperatures and the resulting thermodynamics, a kind of turbo drying occurs with an incomparable efficiency. The evaporation rate per liter of water is around 700W and is therefore at the limit of what is physically possible. Liquid fermentation residue is mixed to approx. 70% moisture via a dry return and mixing screw and fed into the dryer.
After a run of less than 6 minutes, the water content is reduced to a residual moisture of 10% and discharged from the dryer.
Pelleting follows immediately after the drying process.
The dry and dusty fermentation residues are processed into dust-free pellets. These are storable, spreadable and represent an ideal marketing product. Extensive hygienization also takes place through the application of hot gas.
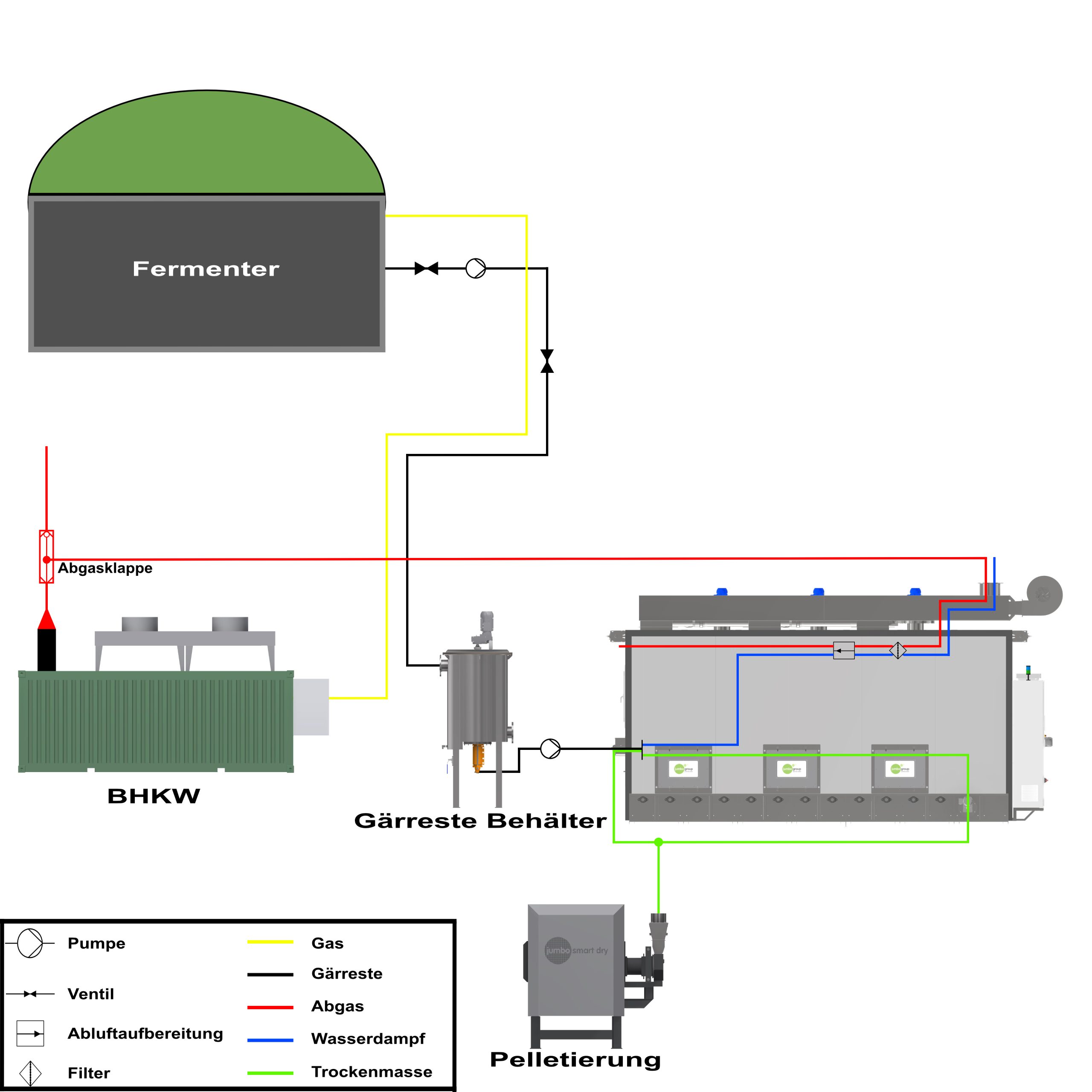